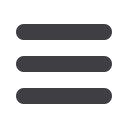
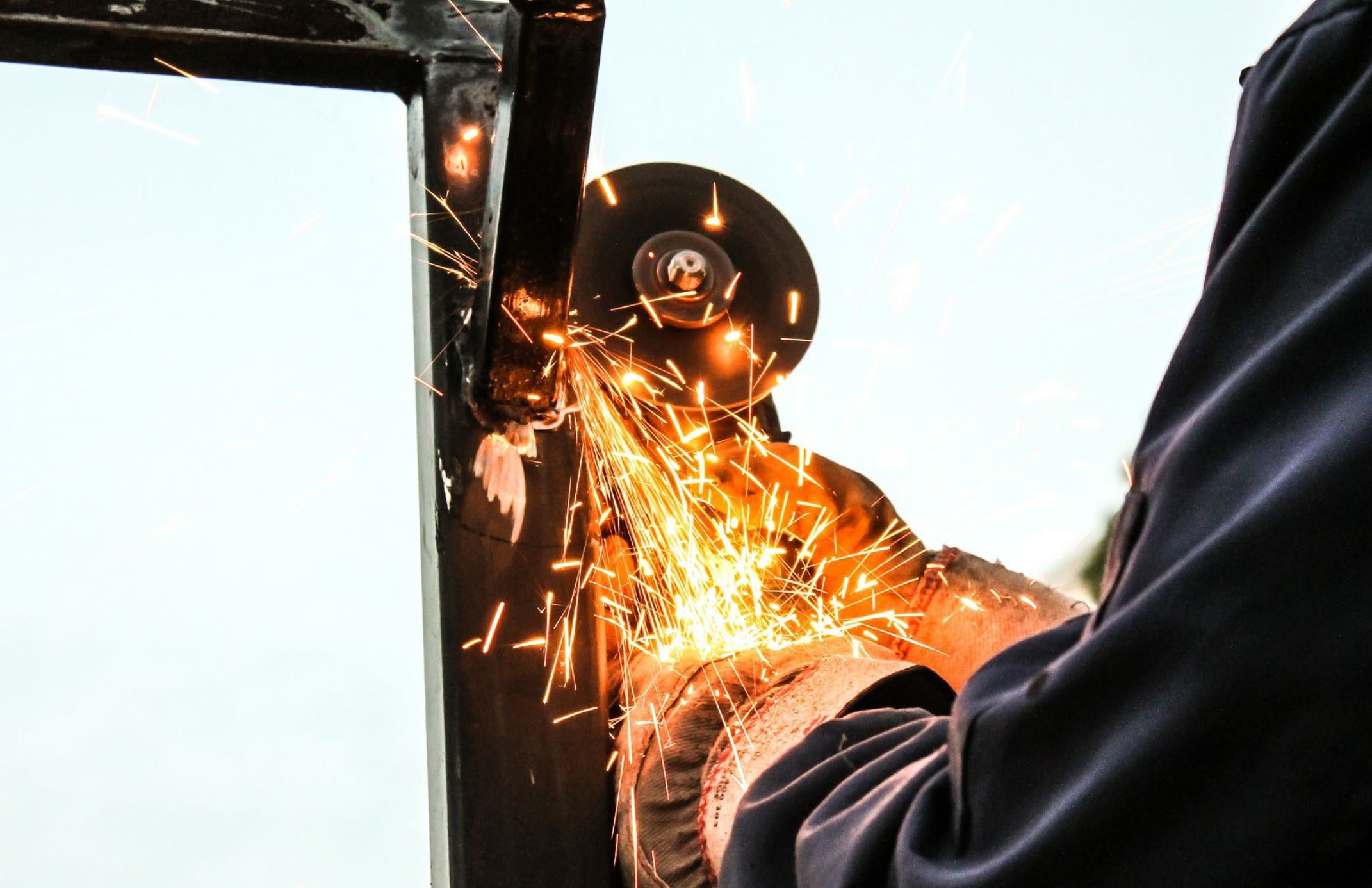
30
31
ACS front loads training in an intensive hands-on
program that includes the use of a training tower, and
pays the apprentice ironworkers as they are learning by
tapping military transition funds, grants, and workforce
development money. The company is founded and man-
aged by veterans. It partners with employers to develop
skilled ironworkers from qualified U.S. military veterans
at no cost to the veteran. Veterans are employed, trained,
and join companies and crews with other veterans. “We
understand that one of the most important factors in
successfully re-integrating to civilian life is a steady pay-
check,” explains Nick Morgan, founder and president. “In
addition, we understand that veterans can fill a critical
labor shortage in the steel erection industry.”
The company,which opened its doors in April 2016, had
already successfully trained and placed more than 100 vet-
erans on jobs performing steel erection activities by the end
of the year.Within sixmonths, the company had achieved
U.S. Department of Labor approval of its ironworker appren-
ticeship program, using the SEAA Ironworker Apprentice-
ship template.According to Morgan,ACS is the largest merit
shop ironworker apprenticeship program in the United
States. In 2017, it is looking to hire 400 ironworker appren-
tices, and expand training locations near military bases in
Oklahoma and Colorado in the central region, in the east in
Georgia,North Carolina, and Pennsylvania, and at western
locations in Oregon and California.
Garrison Steel Erectors, Inc. in Pell City, Ala., recently of-
fered its first hands-on ironworker training class for high
school students, with 22 students from local schools. The
class, currently being led by Garrison Owner and CEO
John Garrison, is many years in the making.
In Alabama, construction owner and contractor groups
began supporting a marketing program called GoBuild Alabama
(gobuildalabama.com) in 2009, which has helped to change
the image of construction in the minds of young people, and
their teachers and parents. Then in 2015, after nearly 20 years
of lobbying, the state legislature passed the Alabama Craft
Training Act, which collects $1 for every $1000 of construc-
tion value on building permits throughout the state. For
instance a $60,000,000 project would generate $60,000
for construction workforce development.
Funds will be managed by the Alabama Craft Training
Board, which will award grants to qualified training
programs. “It is anticipated that as much as $3-5 mil-
lion per year will be available for distribution to ju-
nior colleges and other public and private training
programs,” said Garrison. Collections began in Oc-
tober 2016; funding will be used for craft train-
ing, which is for non-working students; appren-
ticeship training, which is for incumbent
workers wanting to upgrade skills; and
task training, which includes one-
time short term training for
special purposes.