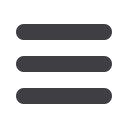
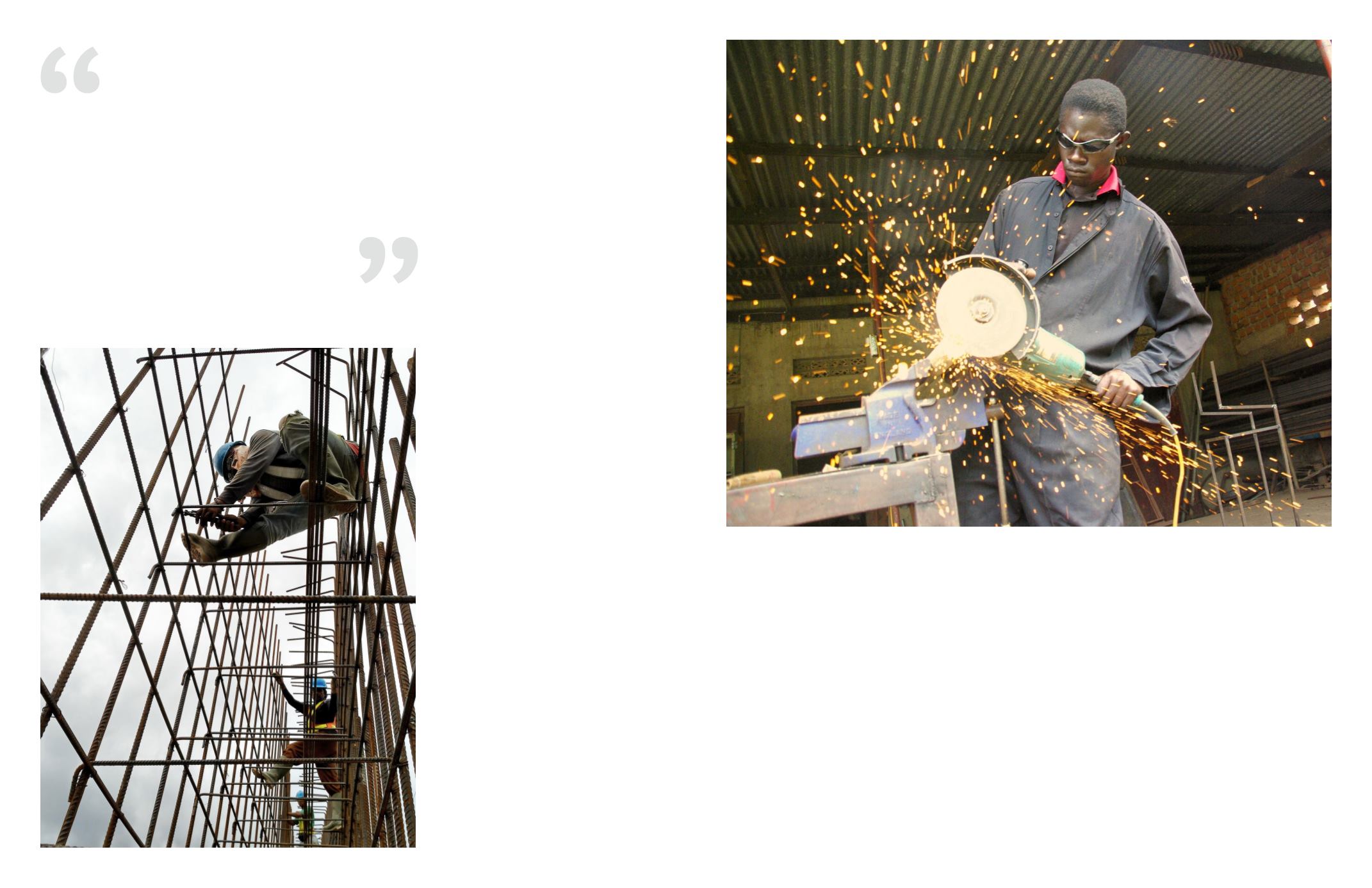
26
27
labor deficit and shifts in learning
styles, we believe craft training
must be fast paced, providing
independent learning opportuni-
ties so that individuals can excel
to become productive employees
early in their career. “Boot camp
style apprenticeship is a popular
trend, providing up to a year of
classroom training and adequate
hours performing critical hands-on
activities before stepping on a job
site,” he said.
The key to success, however, is
providing structured hands-on ac-
tivities and on the job experience.
“Taking time for mastery is an
even bigger challenge for a gener-
ation that wants to move so fast,”
Eldridge adds. “Our current fight
to build a skilled workforce must
also embrace technology. The built
environment becomes more chal-
lenging every day. The new craft
professional must be just as savvy
with technology as with his or her
hands. Knowledge-based learning
will continue to become more and
more convenient as eLearning
technology advances.”
SEAA members understand
that training is not an overnight
solution, but one with long-term
benefits for their companies. “We
are now able to hire new em-
ployees with less experience. In
the past, these are people we might not have
considered,” said Gerald Bickerstaff, MA, QA/QC
Director for Eastern Constructors Inc., Geismar,
La. “Utilizing the SEAA/NCCER ironworker train-
ing program, we can hire employees who need
additional training and teach them the correct
way to perform steel erection, allowing them to
become more efficient ironworkers, while still
creating a safe culture,” he said.
S&R Enterprises, a national structural steel
and precast erector based in Pennsylvania, took
a similar approach on a recent prevailing wage
project in Florida. “We identified as many as
eight workers, who were hired as laborers, but
had the skill and desire to become ironworkers,”
said Josh Collins, PMP, senior project manager
for S&R Enterprises. These were workers who
saw beyond a temporary setback in hourly rates
as an apprentice to the long-term opportunity
to become journeyman ironworkers. Those that
were interested underwent a skills assessment,
then were placed in S&R’s ironworker appren-
ticeship program, where they received class-
room and on-the-job skills based training. S&R
used SEAA’s Ironworker Apprenticeship program,
which meets U.S. Department of Labor, Employ-
Our current fight to build a skilled workforce must
also embrace technology. The built environment
becomes more challenging every day. The new craft
professional must be just as savvy with technology
as with his or her hands. Knowledge-based learning
will continue to become more and more convenient
as eLearning technology advances.
Tim Eldridge
SEAA Craft Training and Assessment Coordinator
and President of Education Services Unlimited